Die Designs that involve the Total Tool Cycle and Optimise Plant and Product Performance.
SERVICES OFFERED
A Die Design Program which examines the Total Tool Cycle
- Examination of entire assembly or Suite of shapes
- View tolerances and fit on related shape
- Reduction ratio-Number of Die Cavities for Optimization.
- Alloy temper requirements
- Mechanical Properties assessed, machining, bending slide-fit etc.
- Assessment of Surface Finish
- Constraints of the Extruder.
- Dies can be manufactured by a Die Maker chosen by CQI or CQI will laisse with the Extruders chosen Die Maker.
Productivity. Full examination of Plant to Optimise Performance
- Billet Size Variations
- Table Length
- Extrusion Speed (Ram Percentage)
- Cooling and stretching requirements
- Packing and evacuations
- Ageing
Product Development
- Assessment of new or existing extruded product
Advice on existing designs or ongoing extrusion problems
- CQI can help examine problems with existing designs or dies and offer correction advice
- This could then be followed by an examination of profile or new design
Training for Die Shop
- Die Shop Managers
- Die Shop Management Team
- Die Maintenance Team
- Learn how to liaise Die Design Team to create Continuous Quality Improvement
- Create a leaner more efficient Die Shop
PROFILE ASSESSMENT
All design initiations begin with a Profile Assessment. Many of our Customer’s will ask for this assessment during their own design inception stage. It is considered best practice to complete Product Development prior to die design.
Our aim is to communicate with the Customer Design Team and promote discussion to examine the long term operation of their product. We later determine the critical dimensions manufacturing dimensions and provide tolerances which reflect the profile applications.
DESIGN FOR MANUFACTURE
The primary aim is to develop a product which services the Customer’s long term needs and allows the Extruder to provide reliable supply. This practice also increases the success rate of prototype extrusion.
In short, Design for Manufacture. The aim of the DFM process is to decrease development stages. These guidelines are an excellent model for reliable design but design evolution and adaptations must be made to suit the vast range of profile which is common in the Extrusion Industry.
During the design construction all aspects are scrutinised and discussed by a team of designers and other trained associates. This design collective helps to avoid mistakes but more importantly motivates collaborative and creative design while avoiding the drawbacks of singular minded design work.
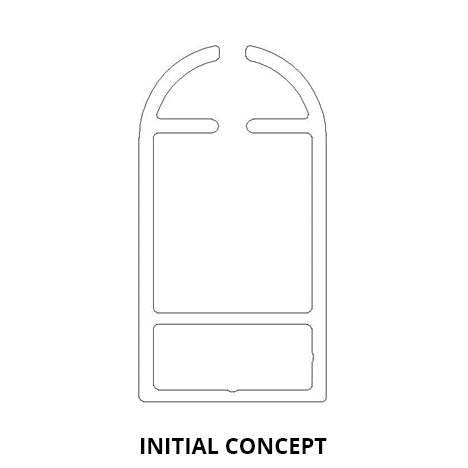